5 Common Manufacturing Outsourcing Errors and How to Avoid Them
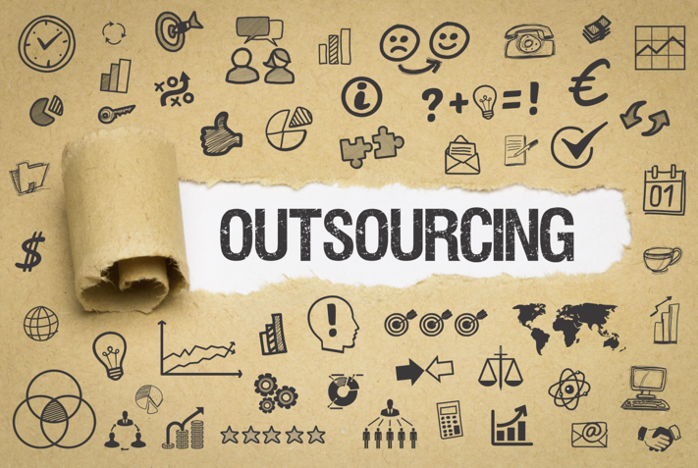
Did you know 70% to 80% of manufactured products are outsourced?
Many businesses outsource to get the product manufacturing they need at a lower cost. It also means these businesses can focus on their core competencies while the outsourcer focuses on manufacturing.
Outsourcing can be a godsend of a solution if you go about it the right way. But what issues can sour the company-manufacturing partner relationship?
Consider these five common manufacturing outsourcing errors and how to avoid them.
1. Miscommunication With Manufacturing Partner
One of the primary sources of tension between a client and an outsourcer is miscommunication. Unless both parties know what to expect of the other and can come together to discuss issues and concerns, there will be problems.
If you outsource manufacturing, ensure there’s open, two-way communication.
Before choosing a manufacturing partner, you must do your homework to find an outsourcer committed to meeting or exceeding customer expectations. It also needs to communicate well and be accessible.
2. Inadequate Focus On Geopolitical Risks
Before choosing a manufacturing partner in another country, you must consider geopolitical risks.
While many businesses outsource to take advantage of the lower labor cost in other countries, these savings can be eaten up if you’re hit with import tariffs or transportation expenses you hadn’t previously considered.
The top country for outsourcing product manufacturing is China. As long as you do your homework, a manufacturing partner in China can be just what your company needs.
3. Quality Control Issues
Costs can go through the roof if you don’t stay on top of quality control issues.
Before you sign a contract with a manufacturing partner, request that the would-be manufacturing partner performs a sample production test. You’ll want to iron out any problems sooner rather than later to avoid costly problems.
4. Rush to Sign an Agreement
It’s never a good idea to sign any agreement before carefully combing over it.
If you sign on with a manufacturing partner too quickly, you could face:
- Substantial manufacturing outsourcing expenses
- Poor quality control measures
When you understand how outsourcing works, you can make informed decisions.
5. Not Staying Involved
Disengaging the process is a mistake even if you find a reputable manufacturing partner. Instead, you need to remain involved throughout the process.
Just because the outsourcer is responsible for manufacturing doesn’t mean you’re relegated to the sidelines. You need to ensure that everything—at all stages of production—is going according to your specific requirements.
Staying involved means you can verify that the finished product meets your quality standards. And if there are any issues, you can detect them sooner rather than later and bring your concerns to the attention of the outsourcer.
Avoid These Common Manufacturing Outsourcing Errors
If your business needs help with manufacturing products, going the outsourcing route can be beneficial. But you’ll want to avoid the common manufacturing outsourcing errors mentioned above.